Jak to funguje?

Navrhneme kontrolní stanoviště, nebo i kompletní robotizované pracoviště podle potřeb Vaší výroby.

Kamery s vysokým rozlišením, laserové snímače a jiné měřící přístroje nashromáždí potřebná data. Pomocí strojového vidění a umělé inteligence vyhodnotíme, zda je daný výrobek v pořádku nebo ne.

Vyhodnocená data ukládáme na zabezpečené servery v Cloudu nebo on premise. Získáte kompletní evidenci výroby.

Výsledky kontrol zpracováváme do přehledných statistik, které zpracováváme každému zákazníkovi na míru.

Průběžně získávané statistiky slouží jako základ pro analýzu a následnou optimalizaci procesů výroby.
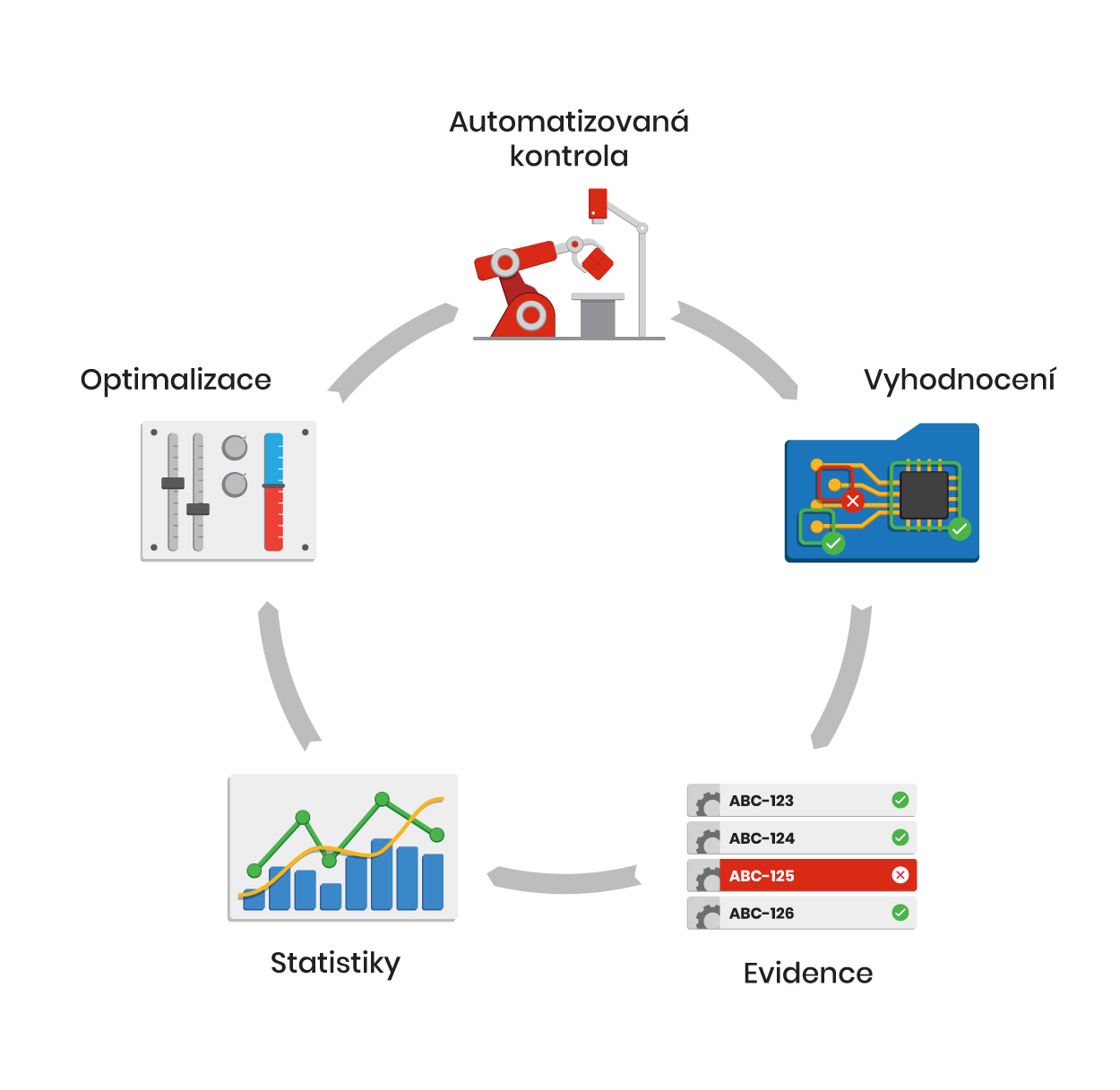